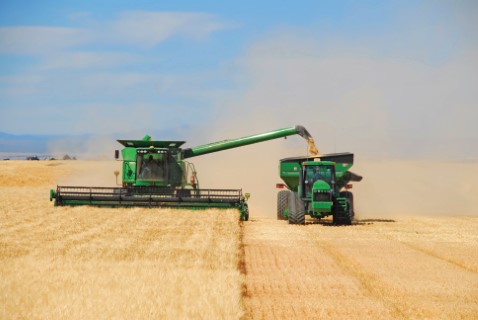
Aldir Carpes Marques Filho
Doutor em Engenharia Agrícola e professor – Departamento de Engenharia Agrícola – Mecanização Agrícola – Universidade Federal de Lavras (UFLA)
aldir@ufla.br
Embora a agricultura seja praticada desde o período que compreende de oito a 10 mil anos atrás, a mecanização agrícola teve seus grandes impulsos tecnológicos após a revolução industrial e a invenção do motor à combustão interna, nos séculos XVIII e XIX.
Nesta fase, a sociedade passou a adotar as máquinas para a realização das atividades industriais repetitivas e de larga escala. Logo em seguida, as primeiras máquinas chegaram ao campo e contribuíram para o aumento da eficiência das operações agrícolas, inicialmente aplicadas em atividades de preparo do solo e, posteriormente, na colheita.
Desde os primórdios da agricultura mecanizada, as máquinas de colheita apresentaram desafios referentes ao manejo, configuração e regulagens dos sistemas de limpeza e separação. Portanto, ao longo dos anos foram surgindo diversos modelos de máquinas e sistemas adaptados à realidade, manejo e morfologia das culturas agronômicas.
As primeiras trilhadoras estacionárias necessitavam que a colheita fosse realizada em uma operação independente e, somente após a retirada do material da lavoura, este fosse conduzido para o sistema de trilha de forma manual ou semimecanizada.
Recentemente as colhedoras de grãos realizam esse processo de forma unificada, reduzindo muito o tempo e a necessidade de mão de obra.
Características das colhedoras autopropelidas
As máquinas de colheita de grãos autopropelidas são verdadeiras indústrias sobre rodas, ou seja, são responsáveis por cortar, retirar o material vegetal do campo, separar a fração vegetal dos grãos, realizar a limpeza destes e armazená-los em um reservatório específico (Figura 1).
Estas máquinas possuem motor próprio e são classificadas de acordo com seu sistema de trilha, que pode ser do tipo radial, axial ou híbrido. Na realidade, essa classificação se dá em função da forma com que a máquina realiza a separação dos grãos do restante do material vegetal e da posição dos dispositivos de trilha em relação à máquina.
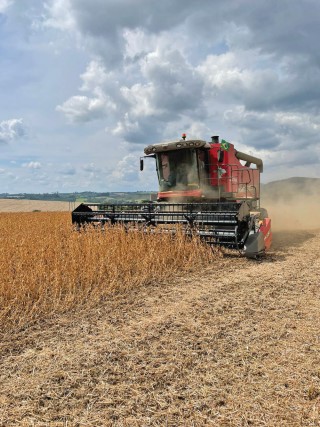
As colhedoras autopropelidas radiais, também chamadas de “convencionais”, possuem normalmente um cilindro localizado na direção perpendicular da máquina, de forma que, após a plataforma de corte e alimentação, o material vegetal passa entre o cilindro radial e o côncavo (que é uma espécie de grelha separadora), recebendo impactos que fazem a debulha dos grãos.
Em seguida, no interior da máquina, o material vegetal é deslocado para um dispositivo chamado de “saca-palha”, ou para peneiras, e estas realizam a separação entre grão e palha pela ação da agitação e da gravidade.
Nas colhedoras de fluxo axial, o cilindro de trilha é instalado longitudinalmente em relação ao chassi da máquina, sistema denominado de rotor axial. A diferença deste sistema para o convencional consiste em manter o material vegetal por mais tempo em contato com os mecanismos de trilha, favorecendo uma debulha mais suave.
Isso permite a diminuição do impacto mecânico sobre o material colhido, pela menor intensidade de contato na trilha. Essas máquinas são as preferidas dos agricultores que colhem lavouras de sementes, devido, principalmente, ao menor dano causado ao material propagativo.
Existem, ainda, colhedoras que combinam os sistemas axiais e radiais de trilha. Essas máquinas são conhecidas como máquinas híbridas, contendo o sistema radial e axial em uma mesma máquina.
As máquinas com sistemas híbridos possuem normalmente alta capacidade de processamento e permitem aos produtores uma liberdade maior de regulagens em função do porte das lavouras.
Manutenção em dia é fundamental
Toda máquina e sistema mecânico apresentam ao longo de seu período de uso, necessidade de intervenções, seja para lubrificação, manutenção preventiva dos órgãos ativos, peças móveis e mecanismos de força, ou mesmo manutenções corretivas para resolver problemas imprevistos.
A manutenção, quando corretamente realizada, é uma das principais formas de se obter o máximo rendimento das máquinas, já que estas permanecem com maior disponibilidade ao longo das operações.
Os custos de manutenção, incluindo mão de obra e peças de reposição, são consideravelmente baixos se comparados com os benefícios alcançados, os quais se expressam por meio de custos operacionais menores e maior produtividade.
O primeiro passo para o sucesso no momento da colheita é manter a manutenção da colhedora em dia. A manutenção pode ser preditiva, preventiva ou corretiva. As manutenções preditiva e preventiva buscam solucionar os problemas antes que eles ocorram, no entanto, se forem muito intensivas, podem ser de alto custo e geram o risco de substituir ou condenar componentes que não estão com defeito ou que suportariam trabalhar por mais tempo.
A manutenção corretiva consiste em reparar ou substituir os componentes por quebras ou falhas (após a ocorrência). Esta forma de manutenção normalmente é mais onerosa, pois pode parar a operação de colheita no instante de sua execução, causando prejuízos econômicos significativos.
O momento ideal para fazer as manutenções nas colhedoras é durante as entressafras, quando a máquina está ociosa. Assim, os produtores têm mais tempo para encontrar peças de reposição e componentes com melhores preços, além de não prejudicarem uma operação em andamento.
Com a manutenção em dia, os sistemas mecânicos tendem a funcionar de forma eficiente durante as operações, minimizando possíveis prejuízos.
As colhedoras necessitam de revisão, manutenção e lubrificação nos sistemas de corte, trilha, separação e limpeza. O sistema de “corte e alimentação” é composto pela plataforma, molinete ou carretel, caracol ou rosca sem fim e pelo elevador de alimentação da trilha (condutor).
Em média, 80% das perdas causadas pela máquina no momento da colheita são por falhas na alimentação. A velocidade do molinete, o espaçamento do caracol e o ajuste da altura da barra de corte em relação à cultura vegetal são pontos que devem ser analisados e ajustados (Figura 2).
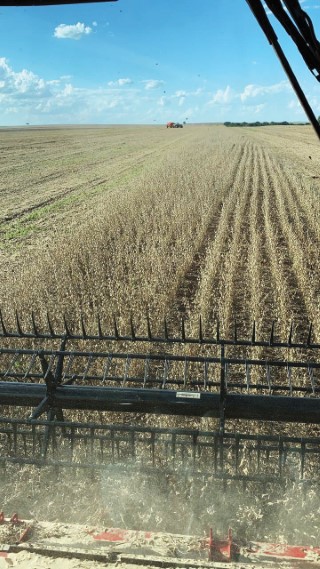
Nas máquinas modernas, equipadas com cabine fechada e sensores, é possível que o operador da máquina acompanhe todo o processo de corte durante o direcionamento da máquina e atue nos ajustes necessários. Sensores de monitoramento interno servem de suporte para ajustes nos mecanismos e fornecem informações para o operador pelo monitor de colheita.
Após a utilização destas máquinas, é preciso realizar a limpeza e calibração de seus sensores internos. Sensores de produtividade (placas de impacto e ópticos), sensores de umidade; sensores ópticos de monitoramento interno do sistema industrial devem ser periodicamente avaliados e testados, pois fornecem informações fundamentais para a tomada de decisão e gerenciamento da operação.
Controle rigoroso da máquina durante a operação
Nas plataformas para colheita de soja, a altura deve ser ajustada para que colete as vagens mais baixas, sem captar material vegetal em excesso na lavoura. O molinete deve ser regulado para tocar a soja no seu terço superior, evitando a debulha natural.
A rosca sem fim, que serve para conduzir o material até o centro da plataforma, conhecida como “caracol”, precisa ser regulada para transportar as plantas de forma suave até o alimentador central.
Se a distância entre o caracol e o fundo da plataforma for muito reduzida, ocorrerão debulhas no sistema de alimentação, principalmente se o ponto de maturação da lavoura estiver adiantado.
Novidades
Novas plataformas têm surgido no mercado, substituindo o antigo caracol por uma esteira deslizante, que conduz o material ao centro da máquina com menor impacto, de forma amena e uniforme.
Estes mecanismos são conhecidos como sistema de condução “drapper” ou “cortina”. Os desafios destas plataformas consistem em manter a qualidade da colheita em áreas com preparo de solo deficiente e com a presença de pedras, tocos e restos vegetais, pois são plataformas que possuem sistemas sensíveis.
A esteira elevadora (alimentador), localizada no centro da plataforma de corte, com a função de elevar o material até a trilha, também conhecida como “boca da colhedora”, exige alguns cuidados, principalmente no que se refere ao ajuste da tensão da sua esteira metálica, pois velocidades excessivas sobrecarregam o sistema de trilha, causando mais perdas nas etapas posteriores, e esteiras com folgas podem debulhar grãos no alimentador.
O material vegetal que foi cortado e conduzido para o centro da máquina pelo alimentador é direcionado para o sistema industrial (trilha, separação e limpeza). Nesta etapa do processo mecanizado, as perdas são menores, porém, algumas regulagens são importantes, como ajustes nas distâncias entre cilindro e côncavo; velocidade do ventilador e abertura adequada das peneiras.
Os valores ideais de ajuste dos componentes do sistema industrial são variáveis em função do estágio de maturação e porte da cultura colhida, de forma que podem sofrer ajustes em função do horário de colheita e condições atmosféricas, principalmente temperatura e umidade relativa.
No início dos sistemas de trilha, praticamente 70% dos grãos são separados do restante do material vegetal. Este material remanescente é direcionado para os sistemas de separação e limpeza e será processado nas peneiras e sistemas de ventilação.
Velocidades altas do ventilador podem forçar a saída de grãos junto com a palha na zona de descarte da máquina, portanto, é importante acompanhar o material que sai da máquina e verificar constantemente a presença de grãos neste local.
Em relação às peneiras de separação, é importante observar suas relações de abertura com a velocidade do ventilador. A peneira superior deve ser ajustada com abertura levemente maior que a peneira inferior. Já na peneira inferior, somente devem passar os grãos limpos, visto que representam a última etapa antes do graneleiro.
Peneiras muito abertas incrementam pedaços de vegetais e impurezas no tanque graneleiro, no entanto, peneiras muito fechadas ou ajustadas causam maior perda de grãos não debulhados, ou mesmo sobrecarregam o sistema de retrilha.
Na etapa de elevação e armazenamento dos grãos na máquina, os ajustes de tensões das correntes são importantes para evitar folgas, essa inspeção é realizada por janelas específicas em cada modelo de colhedora. A tensão da corrente deve prever uma folga que permita um movimento lateral de poucos milímetros e nenhum movimento vertical.
O processo de ajustes na máquina é sistêmico e complexo
O processo de colheita mecanizada torna-se complexo porque não existe uma configuração única para o bom desempenho da máquina, e não se tem uma receita única para obter bons rendimentos.
Isso ocorre pela interferência das condições atmosféricas, das regulagens dos sistemas mecânicos e das características das lavouras variarem em função de cada região produtiva.
Desta forma, o importante para manter a qualidade da colheita mecanizada é avaliar constantemente a máquina e acompanhar de perto a operação de colheita. É preciso ter em mente que a máquina precisa ser ajustada em função do “momento da colheita”.
Assim, uma máquina que estiver colhendo de forma eficiente em um dia com 22°C de temperatura e 56% de umidade relativa no início da manhã, possivelmente não manterá os mesmos níveis de eficácia quando a temperatura subir para 30°C e a umidade cair para 40%.
A realização de ajustes finos de colheita, em função das condições ambientais, já equipa os sistemas de monitoramento de muitas máquinas comerciais modernas, no entanto, as máquinas mais antigas ainda contam com a expertise dos operadores e acompanhamento constante durante toda a operação.
Visto que as condições ambientais interferem diretamente na qualidade da colheita, não se pode deixar de verificar a calibração dos sistemas eletrônicos e sensores presentes na máquina.
Os sensores de fluxo de grãos, por exemplo, permitem a criação de mapas de produtividade, identificando áreas mais ou menos produtivas na lavoura, e servem como parâmetros para tomadas de decisão posteriores de manejo.
Caso os sensores de produtividade não estejam em perfeito funcionamento, toda a cadeia de manejo que é baseada em partes nessa informação também será prejudicada.
A calibração dos monitores de produtividade é tarefa relativamente simples, porém, demanda algum tempo, e mesmo interesse por parte dos produtores. As calibrações devem ser feitas em talhões homogêneos, fora de cabeceiras ou bordas das lavouras.
Após colher este material e encher o tanque graneleiro da máquina, o mesmo deve ser descarregado em um veículo de carga e pesado na indústria, de forma que este valor real de pesagem deve ser informado ao sistema eletrônico da máquina.
Assim, automaticamente, após quatro ou cinco repetições, o sistema da colhedora ajusta os erros e gera dados mais assertivos (Figura 3).
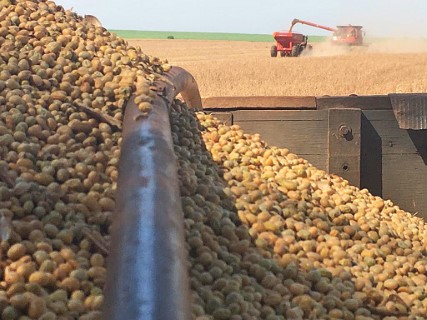
Avaliar e aprimorar, para não perder
Conduzir uma lavoura com excelência até o final do ciclo e perder grãos no momento da colheita é muito frustrante para o produtor. Portanto, é preciso garantir a máxima qualidade nesta operação.
Uma boa forma de avaliar a qualidade da colheita é de forma direta demarcar áreas colhidas e quantificar a matéria-prima presente no campo após a passagem da máquina. Todos os sistemas mecanizados apresentam limitações, porém, sistemas ajustados de colheita e máquinas bem reguladas não podem apresentar perdas maiores que 2%.
Não se pode esquecer que as perdas podem ocorrer por causas naturais, como a senescência das plantas (passar do ponto de colheita), ventos fortes e chuvas. No entanto, estas perdas ocorrem antes da passagem da máquina na lavoura e é preciso separá-las do cálculo das perdas geradas pela colhedora.
O ideal, no campo, seria quantificar as perdas naturais (entrando na lavoura antes da passagem da máquina, demarcando uma área e quantificando os grãos); no sistema de alimentação (quantificando somente as perdas de grãos após a passagem da plataforma), e por fim, quantificar as perdas totais após a passagem da colhedora.
Na prática, muitos pequenos e médios agricultores terceirizam a operação de colheita, pois não possuem uma colhedora disponível. É preciso ficar atento para as condições operacionais, regulagens e qualidade do processo, já que, em sistemas mecanizados “terceirizados”, em que o pagamento de atividades envolve um custo fixo “por empreitada” ou “por fazenda”, a qualidade da operação pode ser deixada de lado em detrimento do tempo.
O mesmo pode ocorrer em regiões de extensas áreas agrícolas, com pouco tempo disponível para realizar a operação de colheita, situação em que o produtor pode renegar a qualidade da operação em função da janela agrícola estreita.
A realização de colheitas descuidadas e apressadas propicia que grandes quantidades de grãos sejam deixadas anualmente no campo. Pesquisas recentes indicam que as perdas totais na cultura da soja giram em torno de 1,5 milhão de toneladas por safra, o que, nos valores atuais da soja, alcança valores econômicos significativos para o País.